Injection molding is a widely used technique for manufacturing toys, providing a reliable method to produce high-quality, intricate designs. This article explores the step-by-step process of producing injection molding toys, from the initial design to the final product, offering insights into how toy moulds contribute to the creation of these popular items.
The Basics of Injection Molding
Injection molding is a manufacturing process where molten material is injected into a mold to form a solid product once it cools and hardens. For toys, this process involves several key steps to ensure the final product meets both safety standards and design specifications.
Step 1: Designing the Toy Mould
The journey of injection molding toys begins with the creation of the toy mould. This crucial component is a precisely engineered tool that determines the shape and details of the final toy. The design of the mould must account for factors such as material flow, cooling channels, and ease of removal. Advanced CAD (Computer-Aided Design) software is often used to create detailed 3D models of the toy mould, ensuring accuracy and efficiency.
Step 2: Creating the Mould
Once the design is finalized, the mould is manufactured. This typically involves machining high-grade steel or aluminum into the desired shape. The mould is crafted with meticulous attention to detail to ensure that it can produce toys consistently and accurately. This step may also include the installation of cooling systems to manage the temperature of the molten material and enhance the cooling process.
Step 3: Preparing the Injection Molding Machine
With the mould ready, the next step is setting up the injection molding machine. The machine needs to be calibrated to the specific requirements of the toy design. This includes adjusting parameters such as temperature, pressure, and injection speed to ensure that the molten material fills the mould correctly and forms a consistent, high-quality product.
Step 4: Injection Molding Process
During the injection molding process, the chosen material, often plastic or resin, is heated until it becomes molten. This molten material is then injected into the toy mould under high pressure. The material flows into all the intricate details of the mould, taking on its shape as it cools and solidifies. This step requires careful monitoring to ensure that the material fills the mould evenly and that no defects occur.
Step 5: Cooling and Ejection
After the material has been injected and allowed to cool, the mould is opened, and the toy is ejected. The cooling time is critical to ensure that the toy maintains its shape and does not warp. The mould may need to be opened and closed several times during the production run, depending on the design and material used.
Step 6: Post-Processing
Once the toys are ejected from the mould, they may undergo various post-processing steps. This can include trimming excess material, painting, and applying decals. Any defects or imperfections are addressed during this stage to ensure that the toys meet quality standards.
Advantages of Injection Molding Toys
1. High Precision
Injection molding allows for precise and intricate designs, which is essential for creating detailed and functional toys. The accuracy of the toy mould ensures that each toy is consistent with the design specifications.
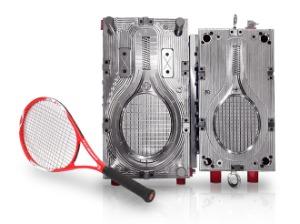
Toy Racket Mold
2. Efficiency
The process is highly efficient, capable of producing large quantities of toys quickly. This is beneficial for meeting market demand and reducing production costs.
3. Durability
Toys produced through injection molding are typically durable and robust. The process ensures that the toys can withstand regular use without easily breaking or deforming.
The production of injection molding toys involves a complex and fascinating process that starts with the design of the toy mould and ends with a finished product ready for the market. Understanding each step provides valuable insight into how these toys are made and highlights the precision and efficiency of injection molding as a manufacturing technique.
Contact Us