The commodity mould market is evolving rapidly, with two major forces driving change: the increasing demand for customization and the need for high-efficiency production. As industries expand and customers seek more personalized products, commodity mould manufacturers are adapting to provide tailored solutions while maintaining productivity. In this article, we'll explore the latest trends shaping the market and how plastic moulding suppliers near me are responding to these demands.
The Rise of Customization in the Commodity Mould Market
Customization has become a defining trend in today's commodity mould market. Whether in packaging, consumer goods, or industrial applications, companies are looking for moulds that can accommodate unique designs, specific product dimensions, and even brand aesthetics. This shift towards custom solutions is reshaping how mould manufacturers operate.
Increased Flexibility
Mould makers now need to offer greater flexibility in their designs. Instead of producing standard, mass-market moulds, they are required to cater to individual client needs. This means developing commodity moulds that can handle variations in shape, material, and size, which is crucial for industries like food packaging or household products where distinctiveness is important.
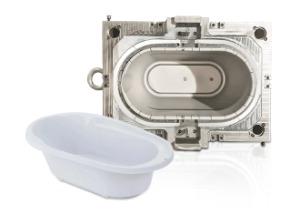
Water Bucket Molds
Smaller Batch Production
The demand for smaller production runs has also increased as companies seek to test new product designs or target niche markets. This means plastic moulding suppliers near me must be able to quickly modify or adjust their moulds to support smaller production runs without sacrificing efficiency or quality.
Efficiency: A Key Focus for Commodity Mould Manufacturers
While customization is important, maintaining high production efficiency remains a top priority for commodity mould manufacturers. Clients still expect moulds that can produce large volumes of products quickly and cost-effectively. The ability to balance customization with efficient production is a key challenge in the market today.
Advanced Manufacturing Technologies
One way manufacturers are addressing this challenge is by incorporating advanced technologies like automation and 3D printing. Automation helps speed up the mould-making process, allowing for faster production cycles. Meanwhile, 3D printing is increasingly being used to create complex, customized moulds in less time than traditional methods.
Durability and Precision
High-quality commodity moulds are designed for durability and precision. This ensures that they can withstand high production volumes without wearing out or causing defects in the final product. Many plastic moulding suppliers near me are investing in durable materials like hardened steel or advanced plastics that not only enhance the longevity of the mould but also improve the quality of the products produced.
How Plastic Moulding Suppliers Are Meeting Customization and Efficiency Needs
To stay competitive in this evolving market, plastic moulding suppliers near me are taking steps to integrate both customization and efficiency into their operations. Here's how they are adapting:
Offering Tailored Services
Suppliers are expanding their range of services to include design consultation and rapid prototyping. These services help clients create unique products faster while ensuring that the commodity mould meets their exact specifications. Clients can work closely with manufacturers to develop moulds that align with their product vision.
Investing in Modular Mould Systems
Modular mould systems are becoming more popular as they allow manufacturers to quickly change specific parts of a mould without creating an entirely new one. This not only speeds up the process but also reduces costs, making it easier to accommodate custom orders. These modular systems also contribute to faster turnaround times, which is especially important in high-demand industries.
Energy-Efficient Production
Efficiency isn't just about speed—energy-efficient production is also a priority. Many suppliers are adopting energy-efficient machinery that reduces operational costs while maintaining production capacity. This makes high-volume commodity mould production more sustainable and cost-effective in the long run.
Real-World Applications of Customized Commodity Moulds
The growing demand for custom solutions is evident across various industries. Here are a few examples of how commodity moulds are being used to meet specific industry needs:
Food Packaging
Companies in the food packaging industry are looking for moulds that can create distinct, branded containers. From specialized shapes to logos embossed on packaging, plastic moulding suppliers near me are developing custom solutions to meet these unique requirements.
Consumer Electronics
The electronics industry often requires moulds with high precision to accommodate small, intricate parts. Custom commodity moulds help manufacturers produce components that fit perfectly into devices while maintaining a sleek design.
Automotive Parts
In the automotive sector, there's a growing need for moulds that can create lightweight yet durable parts. Customization allows manufacturers to produce components that are optimized for performance while reducing material usage.
Future Trends in the Commodity Mould Market
Looking ahead, several key trends are likely to shape the future of the commodity mould market:
Sustainability
As industries move towards more sustainable practices, the demand for eco-friendly mould materials and production processes will rise. Plastic moulding suppliers near me are starting to explore recyclable and biodegradable materials that align with their clients' sustainability goals.
Smart Mould Technology
Smart mould technology, which integrates sensors and monitoring systems into the mould itself, is becoming more prevalent. This allows manufacturers to track the performance of the commodity mould in real time, helping them identify any issues and improve production efficiency.
Globalization and Local Suppliers
While globalization continues to expand the reach of mould manufacturers, local suppliers remain essential for fast, responsive service. Many businesses prefer working with plastic moulding suppliers near me for quicker turnaround times and easier communication.
The commodity mould market is evolving rapidly, driven by the dual forces of customization and efficiency. As industries demand more personalized products, mould manufacturers must balance the need for custom designs with high-speed production. Plastic moulding suppliers near me are rising to this challenge by incorporating advanced technologies, offering tailored services, and embracing sustainability. As the market continues to grow, these trends will define the future of mould manufacturing, making it an exciting time for both suppliers and customers.
Contact Us