Precision molds such as tool box molds and ventilation grille molds play a vital role in producing durable and high-quality plastic parts. From design to final production, the creation of these molds involves a series of steps, each requiring meticulous attention and advanced technology. This article explores the processes involved in manufacturing these molds, highlighting key techniques such as CNC machining and injection molding.
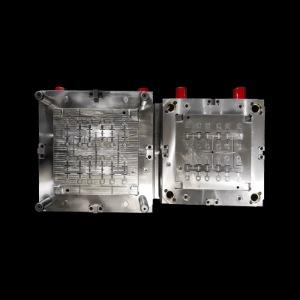
Tile Spacer Molds
Step 1: Designing the Mold
The stage in manufacturing tool box molds and ventilation grille molds is the design phase. This phase sets the foundation for the entire manufacturing process and determines the mold's functionality, durability, and compatibility with specific materials.
CAD Modeling: Both tool box and ventilation grille molds begin with CAD (Computer-Aided Design) modeling. This digital design serves as the blueprint, outlining precise dimensions, shapes, and features. Engineers create detailed CAD models to ensure the mold meets the product's functional and aesthetic requirements.
Simulation Testing: Before moving to production, simulation software is often used to test the design. Simulations help identify potential issues, such as material flow, cooling time, and stress points, that may affect the final product. This process ensures the mold design will perform well during actual production, reducing the likelihood of costly adjustments later on.
Design Adjustments: Based on the simulations and testing, adjustments can be made to optimize the mold's performance. For instance, tool box molds may require reinforced areas to handle heavy items, while ventilation grille molds may need specific vent patterns to ensure efficient airflow.
Step 2: CNC Machining and Mold Fabrication
After finalizing the design, the next step involves CNC (Computer Numerical Control) machining, a crucial process in shaping both tool box molds and ventilation grille molds with high precision.
Material Selection: Molds are typically made from durable metals like hardened steel or aluminum, chosen for their ability to withstand high-pressure injection molding. Tool box molds often require stronger materials due to the higher stress the toolboxes may endure, while ventilation grille molds may use lighter metals depending on product specifications.
CNC Machining Process: CNC machining cuts and shapes the mold cavity based on the CAD model. The machine follows the exact dimensions of the digital blueprint, creating detailed shapes and textures required for the final mold. CNC machining provides high precision, ensuring each part of the mold fits perfectly.
Electro-Discharge Machining (EDM): In some cases, EDM is used to achieve intricate details and tight tolerances that CNC machines might struggle with. EDM uses electrical discharges to mold difficult shapes, allowing for more complex designs in tool box molds and ventilation grille molds.
Step 3: Injection Molding and Mold Testing
Once the mold fabrication is complete, the mold is prepared for the injection molding process, where molten plastic is injected into the mold cavity to create the final product.
Injection Molding Setup: During this stage, the mold is mounted onto an injection molding machine. Molten plastic is injected into the mold cavity under high pressure. For tool box molds, the process must account for thickness and durability, ensuring the final product can bear weight and withstand impact. Ventilation grille molds are designed to create lightweight products with accurate vent spacing for effective airflow.
Cooling and Ejection: After injection, the mold goes through a cooling phase. The plastic cools and solidifies in the shape of the mold cavity. Proper cooling time is essential to prevent warping or deformation, especially in large molds like those for tool boxes. After cooling, the part is ejected from the mold, and the cycle repeats for mass production.
Quality Inspection and Testing: The few samples from the mold are closely inspected to ensure quality. Dimensional accuracy, structural integrity, and surface finish are all checked. For tool box molds, testing includes assessing weight-bearing capacity, while for ventilation grille molds, air flow performance is examined.
Maintenance and Longevity of Tool Box and Ventilation Grille Molds
Regular maintenance of tool box molds and ventilation grille molds is essential for ensuring product quality and extending the mold's lifespan.
Regular Cleaning: Cleaning the mold after each production cycle prevents plastic residue from building up, which could interfere with future molding. Residue buildup can affect the mold's dimensions and ultimately impact product quality.
Lubrication and Storage: Keeping moving parts lubricated prevents wear and tear, ensuring smooth operation and extending the mold's operational life. Proper storage conditions, such as humidity control, prevent rust and corrosion, especially for steel molds.
Routine Inspection: Routine checks for cracks or wear can prevent mold failure. Regular inspection of tool box molds, in particular, helps ensure that heavy loads won't damage the mold over time. Ventilation grille molds, on the other hand, may require more frequent inspections due to their intricate vent structures, which can be prone to clogging or damage.
Advancements in Tool Box Mold and Ventilation Grille Mold Manufacturing
As technology advances, the production processes for tool box molds and ventilation grille molds are becoming more efficient. Modern CNC machines and improved materials are allowing manufacturers to produce molds with tighter tolerances and better durability.
1.High-Speed CNC Machines: The latest CNC machines operate at higher speeds with improved accuracy, reducing production times and allowing for more intricate designs.
2.Enhanced Simulation Software: More sophisticated simulation software is helping engineers create better designs by predicting performance issues before production.
3.Environmentally Friendly Materials: Manufacturers are exploring sustainable materials for mold production and the plastics used in the final products, contributing to more eco-friendly manufacturing practices.
Contact Us